Experience
Project Report
Multi-Stage Distillation
MAJOR FLAVORS & INGREDIENTS COMPANY | NORTHEASTERN US
Problem
Client had a production capacity need to isolate and purify a precursor for further reaction in their process.
History
The client needed to add distillation capacity at their plant to meet the latest market demands and fit the unit into a tight plot within their facility.
Solution
The client requested that ChemPro design a flexible continuous high vacuum distillation system that would concentrate the product without degrading it. The unit needed to handle a range of feedstock variability. ChemPro conducted extensive process simulations to ensure the system could handle the varying feed, operate reliably throughout the feed range and minimize product losses. ChemPro designed, engineered, and built a modular continuous distillation system, incorporating several unique equipment designs to reduce fouling and polymerization of the product at the operating conditions. The unique design included a complex control scheme to ensure the system could operate over a range of feed rates and compositions, reliably prevent contamination of the high purity product by either light ends or heavies, respond quickly to upsets while maintaining product purities and energy efficiency.
Results
The unit has met all process criteria, increased production capacity and conforms to the product requirements for production.
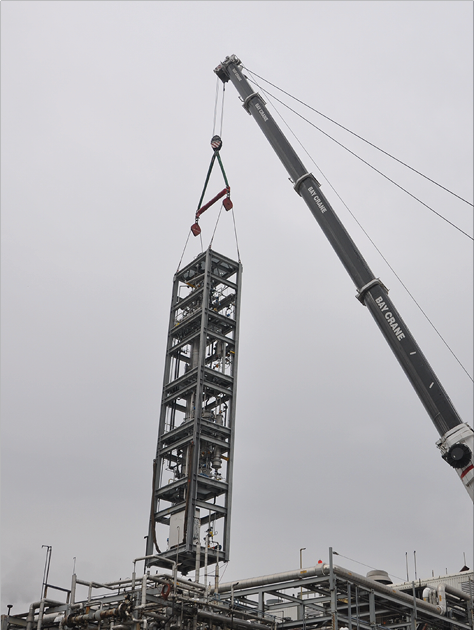
Project Report 250
System
• Modular Distillation System
Structural Frame
• Structural Frame with Stairs
• Galvanized Steel
Equipment
• Column with Sulzer Hi-Efficiency Packing
• Falling Film Reboiler
• Overhead Condenser, ultra low pressure drop design
• Product Side Draw & Bottoms Coolers
• Reflux Tank
• Reboiler Circulation Pump
• Reflux Pump
Piping
• Stainless Steel
Instrumentation
• 316SS Wetted Parts
• Functional specification and logic for Control System